The Essential Guide to Injection Molded Plastics in Modern Business
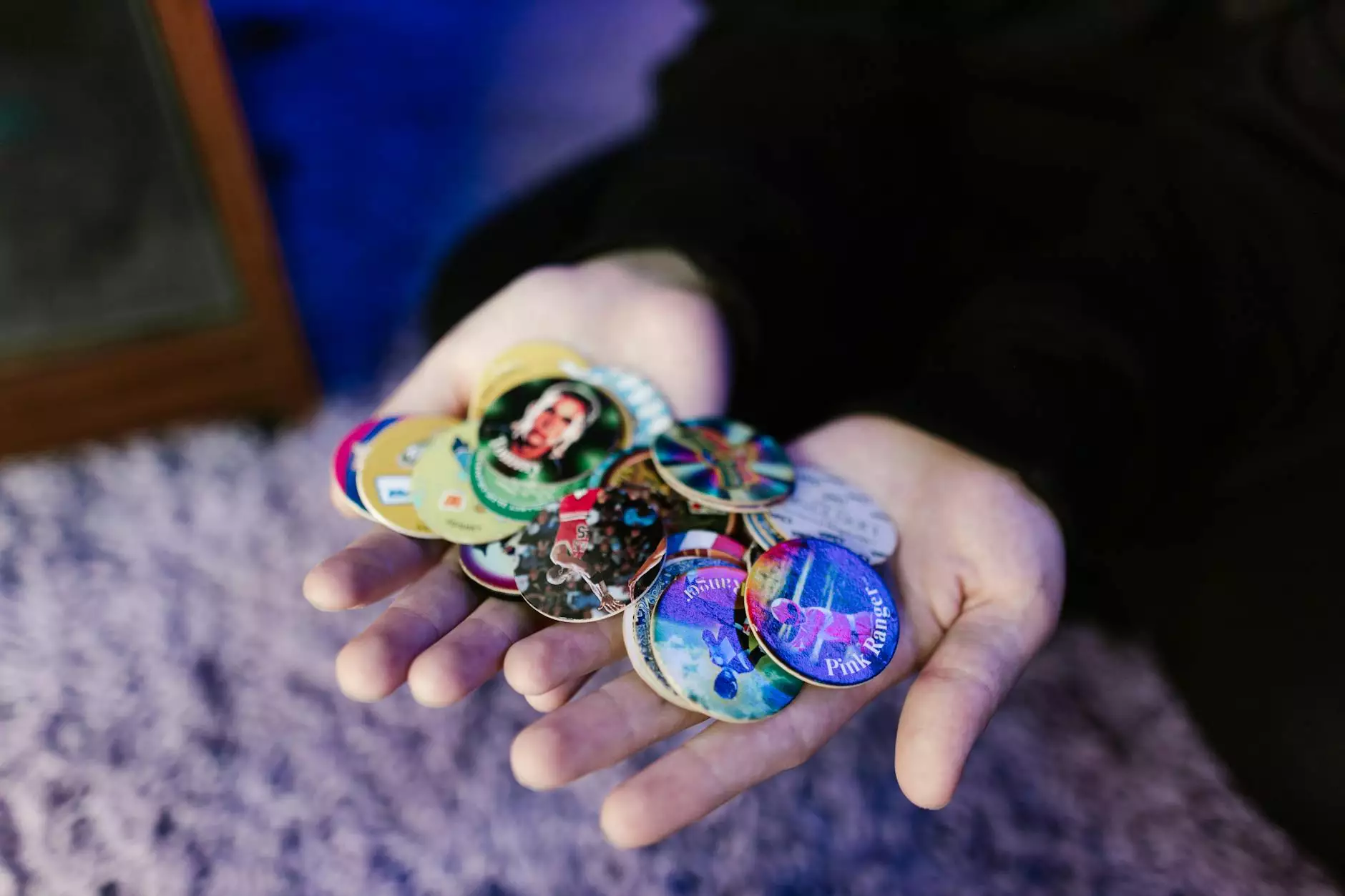
Injection molded plastics have revolutionized various industries, serving as a cornerstone for modern manufacturing processes. This article delves into the intricate details of injection molded plastics, exploring their applications, benefits, technological advancements, and how they can enhance your business's productivity and efficiency. As we navigate through this guide, we will also highlight the pivotal role that DeepMould.net plays in the realm of metal fabrication and injection molding.
Understanding Injection Molded Plastics
Injection molding is a manufacturing process used to produce parts by injecting molten material into a mold. This technique is widely utilized for plastics, allowing businesses to create complex shapes and designs with high precision and minimal waste. Here’s a breakdown of the essential components of injection molded plastics:
- Molds: Precisely engineered tools that form the shape of the final product.
- Materials: Various types of plastics, such as thermoplastics and thermosets, tailored to specific applications.
- Injection Machine: Devices that heat and inject molten plastic into molds.
Benefits of Injection Molded Plastics
Injection molded plastics offer a multitude of advantages that can significantly impact manufacturing efficiency and product quality. Some key benefits include:
- Cost-Effectiveness: High production volumes lead to reduced costs per unit.
- Design Flexibility: Ability to create intricate geometries and complex designs.
- Durability: Plastic components are often more resistant to wear and tear than their metal counterparts.
- Speed: Rapid production cycles make it possible to meet tight deadlines.
- Reduced Waste: The precision of injection molding leads to minimal excess material.
Applications of Injection Molded Plastics
The range of applications for injection molded plastics is vast, impacting various sectors, including:
1. Automotive Industry
Injection molded plastics are used extensively in the automotive sector, contributing to:
- Interior components such as dashboards and trim pieces.
- Exterior parts such as bumpers and fenders.
- Functional components such as clips and connectors.
2. Electronics
From casings to internal components, injection molded plastics are crucial for the production of:
- Smartphones and tablets.
- Home appliances.
- Computer housings and peripherals.
3. Medical Devices
The medical industry relies on injection molded plastics for:
- Disposable syringes and surgical tools.
- Device casings that require sterile conditions.
- Components that ensure reliability and safety in patient care.
4. Consumer Goods
Many household items are produced using injection molding, including:
- Toys and leisure products.
- Containers and packaging.
- Kitchen utensils and gadgets.
The Technology Behind Injection Molding
Understanding the technology involved in injection molding is crucial for businesses looking to optimize their manufacturing processes. Here are some technological aspects:
1. Advanced Materials
The evolution of plastics has led to the creation of materials that are stronger, lighter, and more versatile, such as:
- Polycarbonate: Known for its impact resistance and clarity.
- ABS (Acrylonitrile Butadiene Styrene): Ideal for tough and durable applications.
- PET (Polyethylene Terephthalate): Commonly used for its recyclability and strength.
2. Automation and Robotics
The integration of automation in injection molding processes increases efficiency and reduces labor costs. Robots can handle:
- Material loading.
- Part inspection.
- Packaging and logistics.
3. Simulation Software
Advanced simulation software enables manufacturers to:
- Model and predict the behavior of materials during molding.
- Optimize mold design to minimize defects.
- Reduce the time and cost associated with prototyping.
Choosing the Right Injection Molding Partner
When scaling production with injection molded plastics, choosing the right partner is paramount. At DeepMould.net, we provide end-to-end solutions for metal fabrication and injection molding. Here are key factors to consider when selecting a partner:
- Experience: Look for a provider with a proven track record in injection molding.
- Quality Assurance: Ensure they have robust quality control measures in place.
- Technology: Partner with companies that utilize the latest technology for production and design.
- Customization: Check if they can adapt to your specific needs and offer tailored solutions.
Future Trends in Injection Molding
As industries evolve, so does the landscape of injection molded plastics. Here are some future trends to keep an eye on:
1. Sustainability Efforts
With increasing focus on environmental impact, businesses are seeking:
- Biodegradable plastics.
- Recyclable materials.
- Processes that generate less waste and energy consumption.
2. Smart Manufacturing
The rise of Industry 4.0 is bringing:
- IoT-enabled machinery that streamlines operations.
- Data analytics to enhance decision-making.
- Augmented reality for design and maintenance purposes.
3. Customization and On-Demand Production
Consumers are increasingly looking for products tailored to their needs, leading to:
- Shorter production runs.
- Flexible manufacturing systems.
- Greater involvement of customers in product design.
Conclusion
In conclusion, the role of injection molded plastics in the business landscape is undeniable. Its vast range of applications, coupled with the advancements in technology, make it an essential component of modern manufacturing. By partnering with experienced providers like DeepMould.net, businesses can leverage these advantages to enhance their production processes. As we look to the future, staying informed about trends and innovations in injection molding will be key to maintaining a competitive edge in the market.
Get Started with DeepMould.net
If you're ready to explore how injection molded plastics can benefit your business, contact DeepMould.net today for expert advice and tailored solutions. Let us help you bring your designs to life efficiently and effectively.