Understanding the Importance of Plastic Prototype Manufacturing
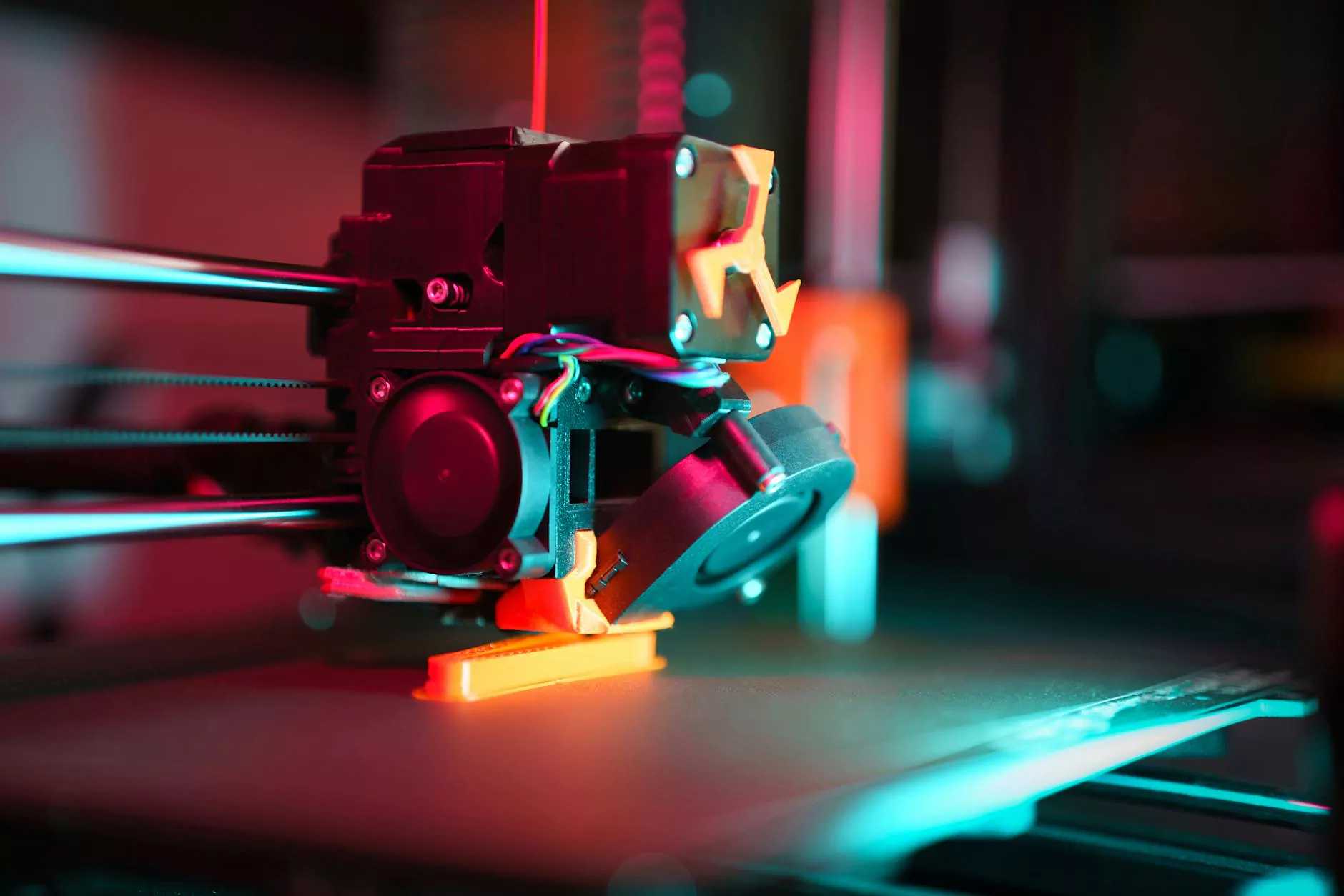
In today's fast-paced industrial landscape, the ability to rapidly create prototypes can determine the success of a product. Plastic prototype manufacturing plays a crucial role in various industries by facilitating innovation, speed to market, and cost-effective production methods. This article delves deep into the realm of plastic prototypes, exploring their manufacturing processes, benefits, and real-world applications.
What is Plastic Prototype Manufacturing?
Plastic prototype manufacturing refers to the process of creating preliminary models of plastic products. Prototypes can be used for testing design, functionality, and usability before committing to full-scale production. Manufacturing these prototypes often involves techniques such as 3D printing, injection molding, and CNC machining.
The Process of Creating Plastic Prototypes
The journey of plastic prototype manufacturing typically involves several key steps:
- Design Phase: Using CAD (Computer-Aided Design) software, designers create detailed drawings of the prototype.
- Material Selection: Choosing the appropriate type of plastic material is crucial. Common materials include ABS, PLA, nylon, and polycarbonate.
- Prototyping Process: Depending on the required precision and cost constraints, different manufacturing techniques are employed.
- Testing and Refinement: Once the prototype is created, it undergoes rigorous testing to assess its functionality and design integrity.
Key Techniques in Plastic Prototype Manufacturing
Different techniques can be utilized for plastic prototype manufacturing, each offering unique advantages and best suited for specific applications. Here are some of the most common methods:
1. 3D Printing
3D printing, or additive manufacturing, is a revolutionary technique that allows for the creation of complex shapes directly from a digital file. This method is popular due to its:
- Rapid production speed
- Cost-effectiveness for small runs
- Ability to create intricate designs
- Reduced waste compared to subtractive methods
2. Injection Molding
Injection molding is a highly efficient production process used for creating large quantities of plastic parts. This technique involves injecting molten plastic into a mold, making it suitable for high-volume production. Its advantages include:
- High precision and repeatability
- Scalability for mass production
- Ability to use various materials
- Excellent finish quality on the surface
3. CNC Machining
CNC machining (Computer Numerical Control) is a subtractive manufacturing process that uses pre-programmed software to control machining tools. This method is ideal for producing parts that require high tolerances and surface finishes. Essential benefits include:
- High precision and accuracy
- Capability to work with hard and soft plastics
- Versatility in creating complex features
- Quick production cycle for low- to medium-volume runs
Benefits of Plastic Prototype Manufacturing
The advantages of utilizing plastic prototype manufacturing are significant and multifaceted. Here are some of the notable benefits:
1. Accelerated Time to Market
Speed is critical in today's market dynamics. Rapid prototyping allows businesses to iterate designs and test user feedback faster, thereby accelerating time to market. This reduced cycle could mean the difference between leading the market and lagging behind competitors.
2. Cost-Effectiveness
Creating prototypes using plastic materials is often less expensive than metal or other advanced materials. Additionally, quicker modifications reduce the costs associated with production delays and redesigns. This cost-effectiveness allows companies to allocate resources more efficiently.
3. Enhanced Design Flexibility
With the capability of making rapid changes to the design after testing prototypes, teams can embrace more innovative ideas without the fear of incurring significant costs. This enhances overall design quality and helps ensure the final product meets market needs effectively.
4. Improved Quality and Reliability
Prototyping allows teams to assess the functionality of their designs before full-scale production. By conducting thorough testing, organizations can identify and fix potential defects early in the process, enhancing the overall quality and reliability of the final product.
Application of Plastic Prototype Manufacturing in Various Industries
The versatility of plastic prototypes makes them invaluable across various industries, leading to substantial advancements and product innovations:
1. Automotive Industry
In automotive manufacturing, plastic prototypes are crucial for testing components such as dashboards, engine casings, and light fittings. These rapid prototypes can significantly reduce development time and lead to better-performing vehicles.
2. Medical Sector
The medical industry relies heavily on prototypes for developing surgical tools, prosthetic devices, and medical equipment. Custom prototypes enable precise testing, enhancing overall safety and functionality in medical applications.
3. Consumer Electronics
Plastic prototypes allow companies in consumer electronics to test new designs for smartphones, computers, and other gadgets. This industry thrives on innovation, and rapid prototyping enables a faster response to consumer demand and market trends.
4. Product Design and Development
For product designers, prototypes serve as essential tools for visualizing and analyzing their concepts. From home gadgets to furniture, having tangible prototypes leads to better presentations and more robust investment proposals.
Choosing the Right Partner for Plastic Prototype Manufacturing
As the importance of prototypes grows, selecting the right manufacturing partner becomes crucial. Look for a partner that offers:
- Advanced technology and state-of-the-art equipment
- Experienced professionals with a solid understanding of design principles
- A positive track record in delivering quality prototypes
- Flexibility in accommodating custom requirements and rapid turnarounds
The Future of Plastic Prototype Manufacturing
The future of plastic prototype manufacturing looks promising, with advancements in materials and technologies shaping the industry. Innovations such as bioplastics and advanced 3D printing methods are likely to play significant roles in sustainability efforts, reducing environmental impact while maintaining efficiency and quality.
Embracing Sustainability
As environmental considerations become more crucial to consumers and businesses alike, the adoption of sustainable practices in prototype manufacturing is on the rise. Companies are increasingly shifting towards recyclable materials, minimizing waste, and utilizing energy-efficient processes. This transition not only benefits the planet but also attracts a customer base that values sustainability.
Integration of Artificial Intelligence
Incorporating artificial intelligence into plastic prototype manufacturing processes will enhance efficiency. AI can optimize design processes, predict potential issues, and streamline production schedules, significantly reducing lead times and costs.
Conclusion
In conclusion, plastic prototype manufacturing is essential in driving innovation and enhancing product development across various industries. By leveraging new technologies and sustainable practices, manufacturers can significantly improve their efficiency, quality, and adaptability. As companies like DeepMould.net embrace these advancements, they position themselves at the forefront of their industries, fostering an environment where creativity can thrive.
The journey of transforming an idea into a reality is a complex one, but with robust and effective prototyping solutions, businesses can achieve remarkable success and capitalize on new opportunities. As the landscape continues to evolve, adapting to the changes in plastic prototype manufacturing will be vital for maintaining a competitive edge.