The Vital Role of an Injection Molding Maker in Metal Fabrication
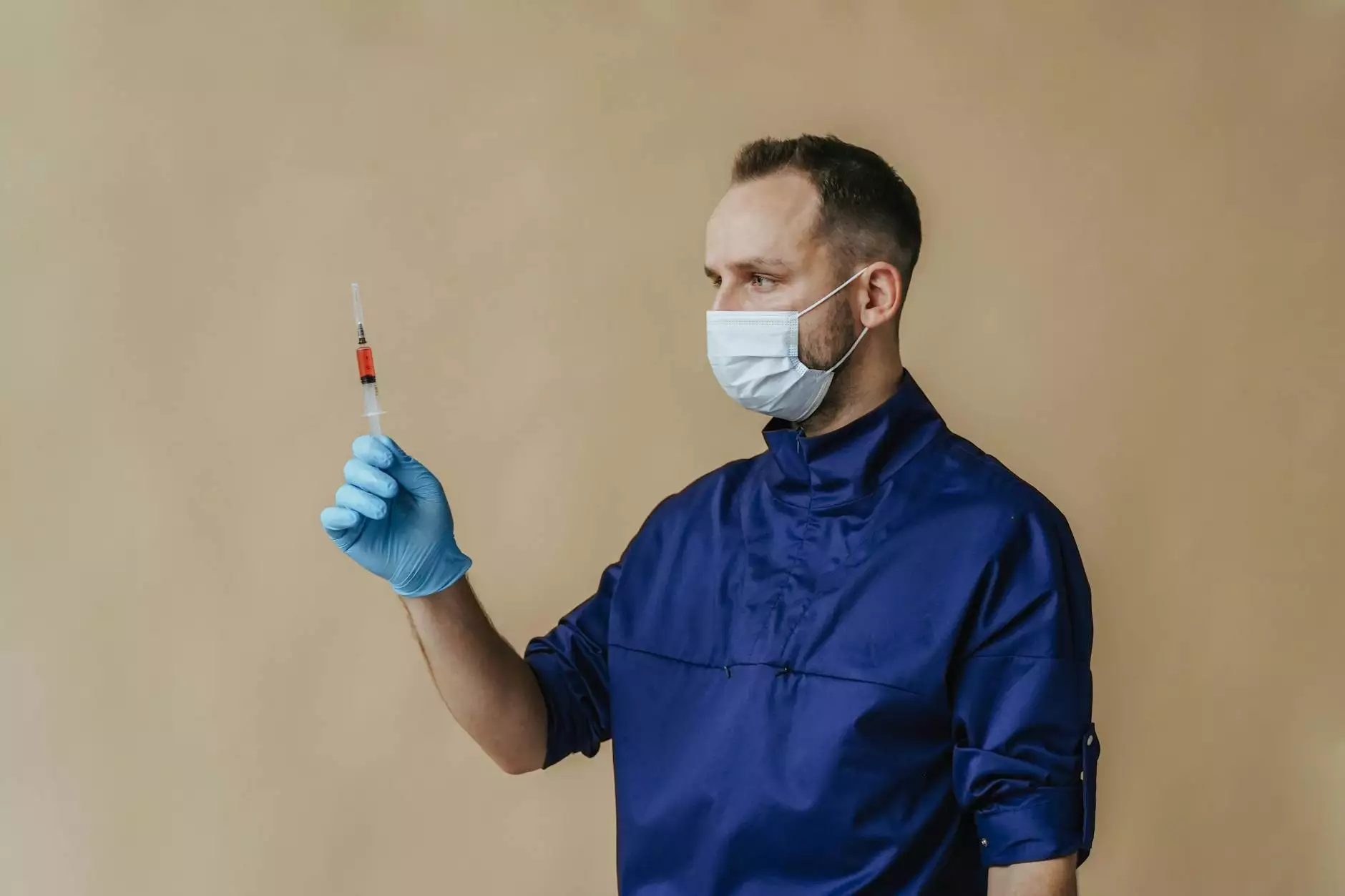
In the world of manufacturing and metal fabrication, the significance of an injection molding maker cannot be overstated. This advanced process has revolutionized how components are produced across various industries, from automotive to consumer goods. At DeepMould, our commitment to quality and innovation positions us as leaders in this field. In this article, we will delve deep into the intricacies of injection molding, highlight how it contributes to efficient manufacturing processes, and outline what sets the best injection molding makers apart.
What is Injection Molding?
Injection molding is a manufacturing process that involves the injection of molten material into a mold to create parts and products. This process is especially prevalent in working with thermoplastic and thermosetting polymers but can also be adapted for metals and other materials. The basic steps involved in injection molding are as follows:
- Material Preparation: The raw material, often in the form of pellets, is first prepped to ensure it can be injected properly.
- Injection: The material is then heated until it becomes molten, at which point it is injected into a mold under high pressure.
- Cooling: The material cools and solidifies within the mold.
- Mold Opening: Once cooled, the mold is opened, and the finished part is ejected.
This process can produce complicated shapes with great accuracy and repeatability, making it an ideal choice for high-volume production runs.
The Importance of an Injection Molding Maker in Metal Fabrication
Injection molding plays a crucial role in metal fabrication, especially when utilizing advanced technologies and materials. An experienced injection molding maker can deliver several benefits including:
- High Precision: Injection molding allows for intricate designs and fine tolerances, making it suitable for applications where precision is critical.
- Material Versatility: Different materials can be utilized simultaneously, allowing for the creation of hybrid products.
- Cost Efficiency: For large production volumes, the cost per unit decreases significantly.
- Speed of Production: The cycle time for injection molding can be very quick, enabling rapid production rates.
Key Considerations When Choosing an Injection Molding Maker
When selecting an injection molding maker, there are several factors you should consider to ensure you partner with the right company:
1. Experience and Expertise
Look for a company with a proven track record in the injection molding field. A seasoned maker will understand the nuances of various materials and processes, which can make a significant difference in the quality of the final product.
2. Technological Advancements
The best injection molding makers invest in the latest technology. This includes advanced injection molding machines and software that optimize the molding process, ensuring consistency and quality.
3. Quality Control Processes
A reputable injection molding manufacturer will have stringent quality control measures in place. This includes regular inspections and testing to verify that every part meets the required standards.
4. Customization Capabilities
Every project is unique, and the ability to customize molds and processes is essential. An injection molding maker should offer tailored solutions that accommodate specific requirements.
5. Customer Support
Reliable customer service is critical. Choose a company that is responsive and willing to work closely with you throughout the manufacturing process.
DeepMould: Your Premier Injection Molding Maker
At DeepMould, we combine cutting-edge technology with extensive industry expertise to deliver unparalleled injection molding services. Here’s what makes us stand out:
State-of-the-Art Facilities
Our facilities are equipped with the latest in injection molding technology, allowing for precise production that meets the most stringent specifications.
Skilled Team
Our team consists of professionals who are not only skilled but are also passionate about delivering quality. From engineers to operators, everyone at DeepMould is committed to excellence.
Sustainability Practices
We recognize the importance of sustainable manufacturing practices. Our processes are designed to minimize waste and recycle materials whenever possible, ensuring we contribute positively to the environment.
End-to-End Service
From design assistance to post-production support, we offer comprehensive services that follow a project from inception to completion.
Applications of Injection Molding in Various Industries
The capabilities of injection molding extend far beyond just basic manufacturing. Here are several sectors where injection molding plays a critical role:
Automotive Industry
In the automotive sector, injection molded components are used in numerous applications such as dashboards, bumpers, and interior trim. The demand for lightweight and durable components makes injection molding an ideal process for automotive manufacturers.
Consumer Goods
Injection molding is widely used in the production of everyday consumer goods, ranging from containers to toys and electronics. The ability to produce complex shapes makes it easier to create innovative products that stand out in the market.
Medical Devices
Medical devices require the highest standards of precision and cleanliness, which can be achieved through injection molding. Components like syringes, surgical instruments, and housings for medical equipment are often manufactured using this process.
Electronics
In electronics, housing and components for devices are often produced using injection molding, benefiting from the material diversity and precision offered by the process. From smartphones to wearables, injected parts are everywhere.
The Future of Injection Molding
As technology advances, the future of injection molding looks promising. Innovations such as 3D printing and advanced robotics are starting to influence how injection molding is approached. However, the fundamental principles of injection molding remain relevant, continuing to evolve with materials that offer improved performance and sustainability.
Moreover, the inclusion of smart technologies such as the Internet of Things (IoT) is expected to play a role in monitoring and optimizing the injection molding process, improving efficiency and reducing waste.
Conclusion
The role of an injection molding maker in metal fabrication is paramount for industries looking to enhance their production capabilities. By choosing a partner like DeepMould, you are not just opting for cutting-edge technology but also for a commitment to quality, sustainability, and customer satisfaction. The future of manufacturing is here, and it is shaped by the precise, innovative processes of injection molding.
Contact us today to learn more about how we can assist you in your next project and elevate your manufacturing operations!