Understanding Machining Lathe Parts Factories: A Comprehensive Guide
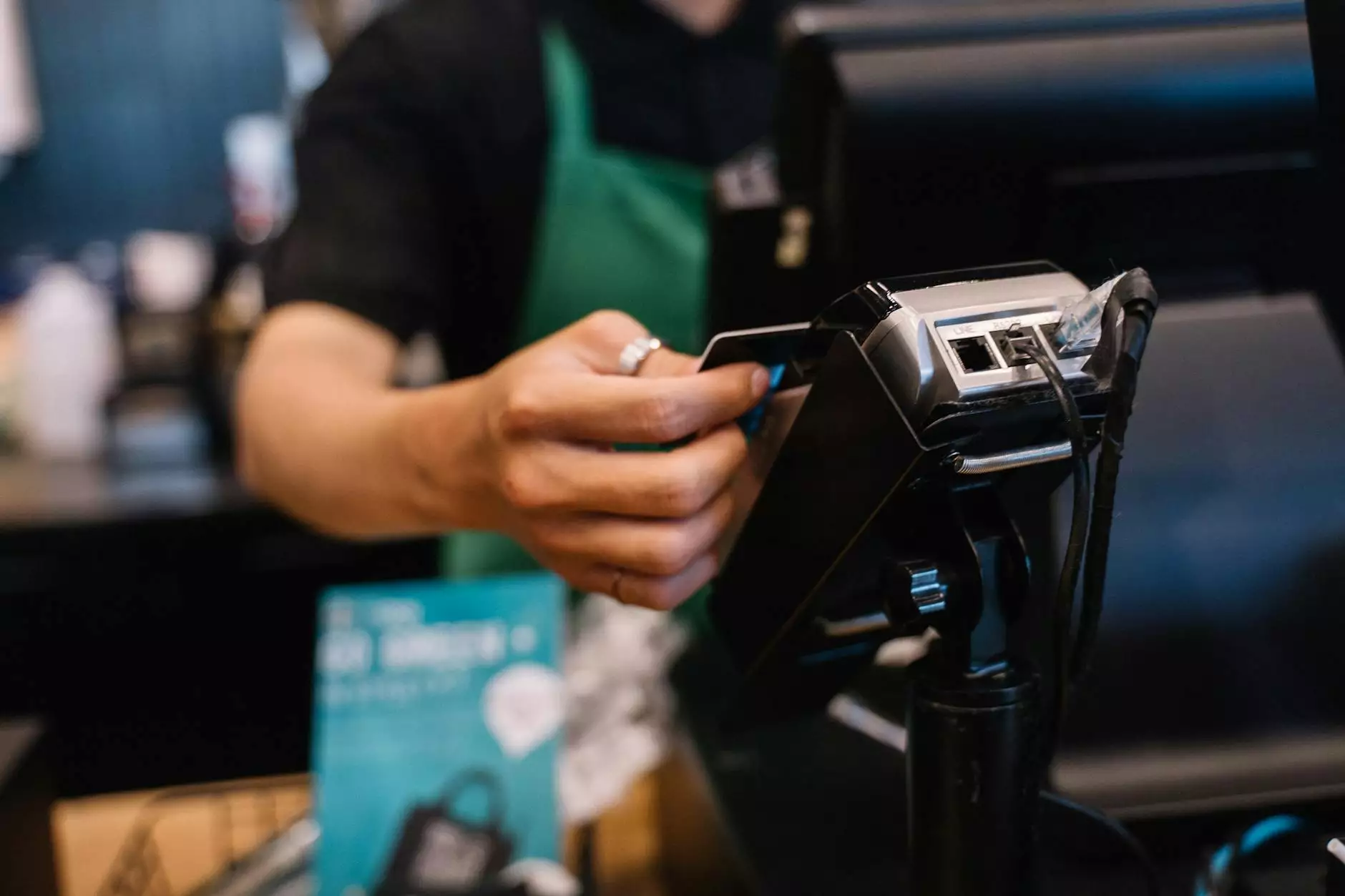
The world of manufacturing is a fascinating landscape filled with innovation and precision. At the heart of this industry are machining lathe parts factories, where metal is transformed into precise components used across diverse sectors, from automotive to aerospace. In this article, we will delve deep into the workings of these factories, their significance in the manufacturing world, and the future trends shaping them.
What are Machining Lathe Parts Factories?
Machining lathe parts factories are specialized manufacturing facilities that focus on producing parts using lathe machines. These machines are essential tools for shaping metal and other materials with high precision.
The Role of a Lathe in Machining
A lathe operates by rotating a workpiece against a cutting tool. This process allows for varied shapes and sizes to be obtained, making lathes versatile machines in the world of manufacturing:
- Cylindrical Parts: Lathes excel at producing cylindrical components, which are vital in multiple assemblies.
- Complex Shapes: Advanced CNC (Computer Numerical Control) lathes can create intricate designs, enhancing a factory's capability.
- Material Variety: They can work with multiple materials, including metals, plastics, and composites, widening the scope of production.
Benefits of Machining Lathe Parts Factories
Manufacturers favor machining lathe parts factories for several compelling reasons:
1. Precision and Accuracy
One of the standout characteristics of lathe manufacturing is its ability to produce parts with exceptional precision. The inherent design of lathe machines ensures that even the most complex geometries can be achieved with minimal errors.
2. High Production Efficiency
With advancements in technology, CNC lathes can operate continuously with minimal human intervention, significantly boosting productivity and reducing lead times for manufacturing processes.
3. Scalability
As demand rises, machining lathe parts factories can easily scale operations. New machines can be added swiftly, and production lines can be adjusted to meet varying requirements without extensive downtime.
4. Cost-Effectiveness
By allowing for the mass production of components with minimal waste, these factories can maintain competitive pricing, which is crucial in today’s market-driven economy.
Key Processes in Machining Lathe Parts Factories
Understanding the main processes adhered to in machining lathe parts factories is essential for grasping how they operate effectively. Below are some of the crucial processes involved:
1. Material Selection
Choosing the right material is the first step in manufacturing. The right metal or composite significantly impacts the final product's quality. Common materials include:
- Steel: Known for its strength and durability, it is widely used for high-performance parts.
- Aluminum: Lightweight and resistant to corrosion, making it perfect for aerospace components.
- Plastic Composites: Ideal for non-metal parts, offering flexibility and resistance to various elements.
2. Machining Process
At this stage, the actual shaping of the workpiece occurs. The most common processes include:
- Turning: The workpiece is rotated while a cutting tool shapes it.
- Facing: A tool cuts the end of the material to make it flat.
- Boring: Internal surfaces are machined to create smooth holes.
3. Quality Control
Ensuring quality is paramount in every factory. Regular inspections and testing are crucial, often utilizing precision measuring tools like:
- Calipers
- Micrometers
- Gauge blocks
Challenges Faced by Machining Lathe Parts Factories
While there are numerous benefits, there are also challenges that machining lathe parts factories face:
1. Skilled Labor Shortage
The demand for skilled machinists is continually rising, and finding qualified personnel can be a challenge in the industry. Investing in training and upskilling programs is essential to address this shortage.
2. Technology Adaptation
With rapid technological advancements, factories must consistently upgrade their machines and processes, which entails significant investment. Those who do not adapt may fall behind their competitors.
3. Environmental Regulations
Factories face increasing pressure to reduce their carbon footprint and manage waste effectively. Compliance with environmental regulations requires additional investment and restructuring of processes.
The Future of Machining Lathe Parts Factories
The manufacturing world is on the brink of transformations driven by innovation. Here are a few trends expected to shape the future of machining lathe parts factories:
1. Automation and Robotics
As automation technology continues to evolve, factories are likely to incorporate more robotics to aid in manufacturing, enhancing efficiency while reducing human error.
2. Advanced Materials
The development of new materials, including superconductors and nanomaterials, will broaden the scope of applications and improve component performance in various industries.
3. Industry 4.0 and Smart Manufacturing
The integration of IoT (Internet of Things) into machinery facilitates real-time monitoring, predictive maintenance, and analytics, significantly improving operational efficiency.
Conclusion
Machining lathe parts factories play a crucial role in modern manufacturing, providing essential components that are foundational to various industries. By embracing technology, prioritizing quality, and addressing challenges, these factories can remain at the forefront of manufacturing innovation. With the continuous advancements in *precision machining*, the future looks bright for any business invested in this space, including esteemed manufacturers like Deep Mould.
As we look forward, the growth of machining lathe parts factories presents not just an opportunity for businesses but also for the industrious workforce dedicated to advancing the manufacturing landscape.